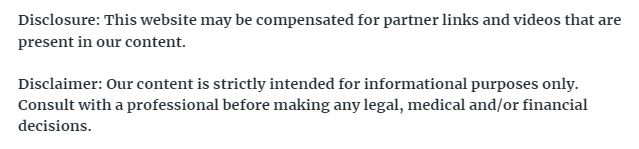
Explore the art and craft of screen printing with our comprehensive guide featuring essential tips and tricks to help you perfect your technique. Whether you’re a beginner or an experienced screen printer, there’s always something new to learn.
1. Gathering Essential Supplies
A successful screen printing setup starts with the right tools, which include a screen, squeegee, and inks. The choice of emulsion is crucial as it defines the longevity and quality of the stencil.
Understanding the characteristics of each supply can improve your printing effectiveness. For example, select inks based on the fabric you’re working with to enhance adherence and durability. Experimenting with different brands and types of essential supplies is a journey of discovery. Finding what works best for your style and projects is part of refining your craftsmanship.
2. Considering Optional Equipment Upgrades
Once you have mastered the basic tools, you might want to consider optional equipment upgrades. Exposure units can enhance your workflow efficiency by providing consistent stencil creation. Automatic presses are a worthwhile investment for scaling up production while maintaining quality. They offer precision and speed, which is beneficial for large-batch printing. Reflect on your current needs to decide if these enhancements are right for you. Evaluating your printing volume and the desired outcome can guide these investment decisions.
3. Understanding Mesh Count
The role of mesh count is vital in determining the detail and quality of your print. A higher mesh count holds less ink, making it ideal for intricate designs. Conversely, a lower mesh count allows more ink to pass through, suitable for bold and heavy designs. Understanding this balance helps in achieving the desired visual effect. Assessing the details of the artwork guides you in selecting the right mesh. Aligning mesh count to design elements ensures cleaner prints and minimal waste.
4. Selecting Mesh for Different Inks
Selecting the appropriate mesh size also depends on the type of ink used. For instance, water-based inks usually require a higher mesh count to prevent excessive ink deposits. Meanwhile, plastisol inks are more comfortable to work with across different mesh sizes due to their thicker consistency. Adjusting mesh according to ink type refines the resolution of your print. Knowledge of how your chosen inks interact with mesh sizes is critical for printing success. This understanding can dramatically enhance the overall quality of your work.
5. Perfecting Your Tension
The tension of your screen is a foundational aspect that impacts the precision of your print. Properly tensioned screens ensure even ink flow and reduce the likelihood of smudging. Inconsistent tension can ruin the sharpness of your prints, making regular checks and adjustments necessary. Utilizing a tension meter can provide reliable results and maintain quality control. Commit to practicing and monitoring screen tension as part of your workflow. This diligence pays off in consistently high-quality outputs.
6. Optimizing Squeegee Technique
Mastering your squeegee technique involves controlling the angle and pressure applied during the print. Consistent pressure helps distribute the ink evenly across the screen. The squeegee angle affects the ink amount deposited, with more acute angles applying thicker layers. Experimenting with these variables lets you tailor the print to your desired opacity and sharpness. Developing muscle memory and control over your squeegee movements is key to professional quality. Practice enhances your ability to adapt techniques to varied designs.
7. Troubleshooting Ink Bleeding
Ink bleeding is a common issue that can disrupt the clarity of your prints. Factors like over-saturation of the screen or misaligned registration contribute to this problem. Preventative measures, such as ensuring precise screen alignment and managing ink volumes, can mitigate bleeding. Maintaining consistent techniques helps streamline production and reduce errors. Understand that troubleshooting involves both prevention and correction. Analyzing your workflow can offer solutions that improve your overall process.
8. Dealing with Screen Blockages
Screen blockages can cause incomplete prints, leading to wasted resources. Residual ink or excess emulsion are common culprits that clog fine mesh holes. Regularly cleaning and properly maintaining screens helps to prevent clogs, as does ensuring correct emulsion application. Utilize screen cleaners to remove stubborn blockages effectively. Maintenance practices should be integral to your routine. Consistent attention to screen condition sustains print quality across projects.
By incorporating these tips and tricks into your screen printing practice, you can enhance your craftsmanship and achieve professional-quality prints every time. Keep experimenting and refining your technique to stay ahead in the dynamic world of screen printing.